Expert UniMac Service Solutions for Commercial Laundry
Commercial laundry businesses need their equipment to work non-stop. Our team has years of experience servicing UniMac systems, including UniMac washing machines and UniMac industrial washers. We know your business success depends on reliable equipment performance.
We provide complete UniMac washer and dryer solutions. Our expert maintenance and repair services will keep your equipment running efficiently. The team's expertise with UniMac laundry systems will give a steady workflow that extends your equipment's life.
This piece covers everything in UniMac service solutions. You'll learn simple troubleshooting and advanced maintenance techniques. We show you how to spot common problems, boost performance, and take preventive steps that reduce future disruptions.
Diagnosing Common UniMac Equipment Issues
Advanced diagnostic tools help us streamline the troubleshooting process for UniMac equipment. The UniLinc Touch system has transformed our approach to equipment problems. It provides error alerts in clear language and eliminates the need to figure out complex UniMac error codes.
Our diagnostic approach employs TotalVue technology to give complete visibility into your laundry operation's performance metrics. The system monitors critical indicators and allows immediate adjustments through cloud-based access.
Common UniMac error indicators include:
-
Door lock malfunctions
-
Water level issues
-
Temperature sensor failures
-
Drainage problems
-
Unbalance detection alerts
Proper documentation plays a key role in the diagnostic process. Our technicians' detailed service records with notes and images are a great way to get insights for future maintenance and repairs.
Safety remains our top priority during equipment repairs. Our team disconnects the power supply completely and waits the mandatory 5-minute period to check for residual voltage. This step protects against high voltage retention in internal components after power-off.
Professional intervention works better than DIY attempts for complex electronic issues or control panel problems. Our certified technicians have specialized training and tools to diagnose and repair sophisticated UniMac systems safely.
The TotalVue monitoring system measures performance indicators quickly. It provides diagnostic reports through a personalized web portal that ensures quick problem resolution. This proactive strategy prevents small issues from becoming major equipment failures.






















Optimizing Equipment Performance
Your UniMac equipment needs a strong maintenance strategy to perform at its best. Our experience shows that preventative maintenance cuts down major equipment downtime and costs.
Here are the key maintenance practices you need:
-
Check equipment carefully at the start and end of each workday
-
Record all issues, alerts, and repairs with detailed notes and photos
-
Follow a strict maintenance schedule
-
Keep machines and areas around them clean
-
Check leak detection systems often
UniLinc Technology will help you improve efficiency. This advanced system cuts water use by up to 39% during rinse cycles and makes cycle times 12% faster than competitor models.
UniMac's 400 G-Force extraction is a big deal as it means that drying times are shorter and throughput increases. OPTidry Technology reduces linen loss by up to 31% and cuts utility and labor costs.
We adjust water levels and temperature settings based on what you need. Our customized ECO Cycles cut water use by up to 30% while keeping UniMac's high wash quality. Our technicians make sure your equipment runs efficiently. Modern laundry systems need specialized knowledge to maintain them properly.
Good documentation and regular checks prevent maintenance tasks from being missed. This proactive approach and our UniMac systems expertise help your laundry operation run smoothly and keep costs low. For optimal performance, always refer to your UniMac washer manual and UniMac dryer manual for specific maintenance and safety tips.
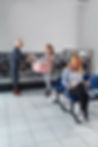

Advanced Troubleshooting Solutions
The advanced UniLinc monitoring system lets us access machine performance data and maintenance logs remotely. We get instant error notifications and detailed performance reports without being at your facility.
The TotalVue system gives us a complete view of key performance metrics at multiple locations. Our cloud-based monitoring platform tracks live data to improve your operation right away.
Here are the advanced error resolution steps we implement for UniMac washer troubleshooting and UniMac commercial dryer troubleshooting:
-
ERR1: Water inlet inspection and pressure verification
-
ERR2: Drainage system evaluation
-
ERR3: Door lock mechanism assessment
-
ERR4: Load distribution analysis
Documentation plays a vital role in our troubleshooting process. Our technicians keep detailed service records with images and maintenance logs. These records are a great way to get support for warranty claims and future reference.
Direct connection to UniMac's expert team at their Wisconsin headquarters provides specialized technical support. This teamwork helps us deliver the latest solutions for your equipment challenges.
Our advanced diagnostic capabilities include wireless networking that monitors and manages your laundry operations remotely. We can spot potential issues early and help you avoid getting hit with expensive downtime.
Note that while remote monitoring systems are powerful tools, some repairs need hands-on expertise. We always suggest working with certified technicians on complex repairs to keep your equipment safe and running longer.
Contact Automated Laundry to Service Your Unimac Laundry Machines
UniMac service makes the difference between occasional equipment issues and reliable performance. The detailed diagnostic tools, including UniLinc Touch and TotalVue technology, give live insights that keep your laundry operations running smoothly.
Each facility has unique requirements and challenges. Automated Laundry Systems has delivered expert sales and service for commercial washers and dryers since 1976. We have developed solutions for coin and on-premises laundry facilities with over 40 years of industry experience.
Our certified technicians are ready to help you achieve optimal results through routine maintenance and advanced troubleshooting solutions. If you need a UniMac repair service, our team is always available to assist you.

FAQs
How long do commercial washing machines typically last?
Commercial washing machines generally have a lifespan of 10 to 15 years. With proper maintenance and care, some machines can even last 20 years or more, making them durable machines and a solid investment for laundry operations.
What sets UniMac equipment apart from other commercial laundry brands?
UniMac equipment stands out due to its advanced features like UniLinc Touch system for easy diagnostics, TotalVue technology for performance monitoring, and innovative solutions like OPTidry Technology that can reduce linen loss by up to 31% while decreasing utility and labor costs. UniMac's washer-extractors and tumble dryers are known for their easy-to-use controls and programmable cycles, offering the lowest total cost of ownership in the industry.
Why is professional servicing important for UniMac equipment?
Professional servicing is crucial for UniMac equipment because modern industrial laundry equipment requires specialized knowledge. Certified technicians have the expertise to diagnose issues accurately, perform complex repairs safely, and optimize equipment performance, which helps prevent costly downtime and extends machine lifespan.
What are some common issues with UniMac equipment?
Common issues with UniMac equipment include door lock malfunctions, water level problems, temperature sensor failures, drainage issues, and unbalance detection alerts. However, many of these can be quickly identified and resolved using UniMac's advanced diagnostic tools and monitoring systems.
How can I optimize the performance of my UniMac laundry equipment?
To optimize UniMac laundry equipment performance, implement a robust maintenance strategy including regular inspections, proper documentation of issues, adherence to maintenance schedules, and keeping machines clean. Additionally, utilize UniMac's advanced features like UniLinc Technology and 400 G-Force extraction to improve laundry efficiency, reduce water consumption, and maximize throughput. Regular maintenance of UniMac parts and service parts is also crucial for optimal performance.